Silicone
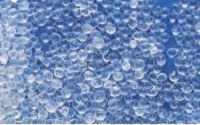
Silicones, also known as polysiloxanes, are polymers that include any inert, synthetic compound made up of repeating units of siloxane, which is a chain of alternating silicon atoms and oxygen atoms, frequently combined with carbon and/or hydrogen. They are typically heat-resistant and rubber-like, and are used in sealants, adhesives, lubricants, medicine, cooking utensils, and thermal and electrical insulation. Some common forms include silicone oil, silicone grease, silicone rubber, silicone resin, and silicone caulk.
Silicones are used in many products. Ullmann's Encyclopedia of Industrial Chemistry lists the following major categories of application: Electrical (e.g., insulation), electronics (e.g., coatings), household (e.g., sealants for cooking apparatus), automobile (e.g., gaskets), aeroplane (e.g., seals), office machines (e.g., keyboard pads), medicine/dentistry (e.g., teeth impression molds), textiles/paper (e.g., coatings). For these applications, an estimated 400,000 tons of silicones were produced in 1991.
Click here for Cjan Silicone Hoses.
Fluoropolymers
Fluoropolymers are ideal for pharmaceutical and biopharmaceutical processing equipment because they have excellent chemical and thermal resistance. Their molecules have continuous non-reactive surfaces and are compatible with virtually all chemicals and solvents. They are far more resistant to chemical attack than conventional chlorinated and hydrocarbon polymers, and have far higher service temperatures.
There are a number of materials in the Fluoropolymer family. PTFE (Polytetrafluoroethylene) is the original Fluoropolymer, discovered by DuPont in 1938. From this original development there have been a number of other materials developed – trying to improve on the difficult processing characteristics of PTFE. These have been more or les successful, having to trade properties of PTFE in order to attain other characteristics. The principal materials used in the industries that we serve are:
PTFE
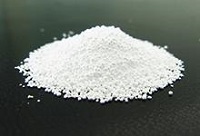
PTFE is not melt-processable and therefore usually needs to be formed into the required shape prior to sintering.
PTFE comprises both carbon and fluorine atoms, as a straight chain molecule, the carbon backbone being protected by a helix of the fluorine atoms wrapped around it. This carbon-fluorine bond is one of the strongest chemical bonds and gives the material its properties of corrosion resistance and non-stick.
PFA
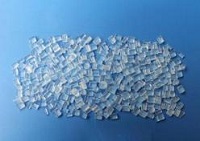
PFA (Perfluoroalkoxy) was developed in order to achieve a true melt processable fluoropolymer. Its characteristics are such that in service it can be considered as interchangeable with PTFE in terms of its chemical service and temperature and pressure duty. It has the highest permeation performance of the fluoropolymers, exceeding that even of paste extruded PTFE. It also provides the smoothest and least wettable finish of all of the Fluoropolymers. Click here to see more related
PFA Lined Fittings.
FEP
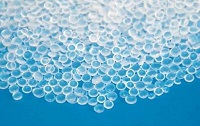
FEP (Fluorinated Ethylene Propylene) is another melt-processable Fluoropolymer. It does not have the almost universal chemical resistance of PTFE and PFA and its maximum operating temperature in service is 150℃. We use the material occasionally for the manufacture of “sheet lined products”. This is essentially a lining made up of sheet and tube elements of FEP welded together in situ. Sheet lining allows one to line complex articles without the use of expensive moulding tools, to cope with the inevitable tolerance errors of welded fabricated steelwork and with the use of bonded linings to provide a degree of vacuum performance. Where the chemical performance and temperature duty are not an issue, the material provides a less expensive alternative to PFA.
PVC
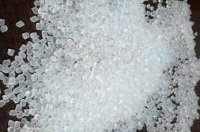
PVC (Polyvinyl chloride), more correctly but unusually poly(vinyl chloride), commonly abbreviated PVC, is the world's third-most widely produced synthetic plastic polymer, after polyethylene and polypropylene.
PVC comes in two basic forms: rigid (sometimes abbreviated as RPVC) and flexible. The rigid form of PVC is used in construction for pipe and in profile applications such as doors and windows. It is also used for bottles, another non-food packaging, and cards (such as bank or membership cards). It can be made softer and more flexible by the addition of plasticizers, the most widely used being phthalates. In this form, it is also used in plumbing, electrical cable insulation, imitation leather, signage, phonograph records, inflatable products, and many applications where it replaces the rubber.
Pure poly(vinyl chloride) is a white, brittle solid. It is insoluble in alcohol but slightly soluble in tetrahydrofuran.
Stainle SS Steel
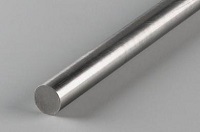
Stainless steel is an alloy of Iron with a minimum of 10.5% Chromium. Chromium produces a thin layer of oxide on the surface of the steel known as the 'passive layer'. This prevents any further corrosion of the surface. Increasing the amount of Chromium gives an increased resistance to corrosion.
Stainless steel also contains varying amounts of Carbon, Silicon, and Manganese. Other elements such as Nickel and Molybdenum may be added to impart other useful properties such as enhanced formability and increased corrosion resistance.
Stainless steels of various kinds are used in thousands of applications. The following gives a flavour of the full range:
-
Domestic – cutlery, sinks, saucepans, washing machine drums, microwave oven liners, razor blades
-
Architectural/Civil Engineering – cladding, handrails, door and window fittings, street furniture, structural sections, reinforcement bar, lighting columns, lintels, masonry supports
-
Transport – exhaust systems, car trim/grilles, road tankers, ship containers, ships chemical tankers, refuse vehicles
-
Chemical/Pharmaceutical – pressure vessels, process piping.
-
Oil and Gas – platform accommodation, cable trays, subsea pipelines.
-
Medical – Surgical instruments, surgical implants, MRI scanners.
-
Food and Drink – Catering equipment, brewing, distilling, food processing.
-
Water – Water and sewage treatment, water tubing, hot water tanks.
-
General – springs, fasteners (bolts, nuts, and washers), wire.
What are multiple certifications?
This is where a batch of steel meets more than one specification or grade. It is a way of allowing melting shops to produce stainless steel more efficiently by restricting the number of different types of steel. The chemical composition and mechanical properties of the steel can meet more than one grade within the same standard or across a number of standards. This also allows stockholders to minimise stock levels.
For example, it is common for 1.4401 and 1.4404 (316 and 316L) to be dual certified - that is the carbon content is less than 0.030%. Steel certified to both European and US standards is also common.